Проблема коррозии, вы знаете, это же просто бич для любой отрасли, где есть металл. Ржавеет всё – от крошечного болтика до огромной металлоконструкции моста. И это не просто некрасиво. Это, главное, опасно. Разрушаются несущие элементы, возникают аварии, да и экономические потери колоссальные. Вот представьте, сколько денег уходит ежегодно на ремонт, замену, восстановление того, что просто-напросто съела ржавчина! Цифры там, конечно, ошеломляющие. Мы же привыкли к чему? Горячее цинкование – это когда деталь окунают в расплавленный цинк. Или гальваника – покрытие тонким слоем цинка из электролита. Ну и, конечно, краска. Красят и красят, правда, не всегда это спасает надолго. Все эти методы, безусловно, работают, но у них есть свои нюансы. Где-то покрытие не очень равномерное, где-то деталь может повести, а где-то просто не добраться до всех уголков. И вот тут на сцену выходит термодиффузионное цинкование, или, как его еще называют, шерардизация. На мой взгляд, это прямо прорыв. И, кстати, если сравнивать с другими способами, то цена на термодиффузионное цинкование часто оправдывается его долговечностью и качеством. А появилась эта технология, ну, она не вчера родилась, конечно. Ее изобрел такой себе Шерард, еще в начале XX века. Так что это не что-то там ультрановое, но активно развиваться и находить широкое применение она начала относительно недавно.
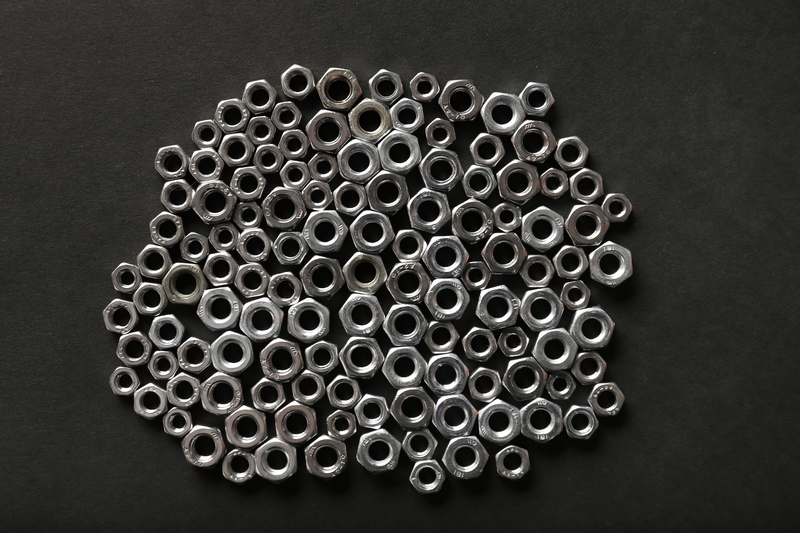
А теперь давайте копнем поглубже и разберемся, как это все работает. Ведь это же самое интересное, правда? В основе лежит, казалось бы, простой принцип – диффузия цинка в поверхностный слой металла. То есть, цинк не просто налипает сверху, как краска, а он, буквально, проникает в структуру стали. Представьте себе, что вы всыпаете сахар в кофе и он там растворяется, перемешивается. Ну, тут, конечно, не совсем так, но смысл похож – образуется единое целое. Это происходит при высоких температурах, но при этом они ниже точки плавления цинка, что важно. Мы имеем дело с порошком, а не с расплавом.
Так вот, когда цинк проникает в сталь, там начинается такая химическая магия. Образуются интерметаллидные фазы Fe-Zn. Что это значит? Это не просто смесь, это новые соединения железа с цинком, которые обладают совершенно уникальными свойствами. Они очень твердые, очень стойкие. Представьте, как будто вы сварили два разных металла в один, который стал суперпрочным. И этих фаз, кстати, несколько, они образуют слои с разным содержанием цинка. Чем ближе к поверхности, тем больше цинка. Температурные режимы, конечно, играют огромную роль. От них зависит, какие именно фазы образуются, какой будет толщина покрытия, какой будет его состав. Малейшее отклонение, и качество может поплыть. Это, ну, как готовить сложное блюдо – нужно выдержать точную температуру.
Теперь пошагово, как это все происходит. Сначала, понятное дело, подготовка поверхности. Тут без этого никуда. Грязь, ржавчина, масло – все это надо убрать. Обычно это делают дробеструйной обработкой, потом обезжиривание, ну и иногда травление. Поверхность должна быть идеально чистой, чтобы цинк мог нормально проникнуть. Затем, изделия, которые нужно покрыть, их загружают в специальные контейнеры. Эти контейнеры заполнены цинксодержащей смесью. Это не просто чистый цинк, там обычно еще есть активирующие добавки, которые помогают процессу идти быстрее и эффективнее. Могут быть инертные наполнители, чтобы порошок не слипался.
Дальше контейнеры отправляются в печь. Там происходит нагрев и выдержка при определенной температуре. Это может занимать несколько часов, в зависимости от того, какую толщину покрытия нужно получить. Во время этой выдержки и происходит та самая диффузия и образование интерметаллидов. После этого – охлаждение. Оно может быть медленным, может быть быстрым, опять же, в зависимости от того, что хотим получить. И уже после этого изделия извлекают. На них, конечно, может остаться немного порошка, так что их обычно очищают от остатков смеси, иногда пассивируют, чтобы еще улучшить коррозионную стойкость. Это, ну, своего рода финишная полировка. Используемые материалы, как я уже упомянул, это в первую очередь цинковый порошок. Важна его чистота, размер частиц – чем мельче, тем лучше он себя ведет. И, конечно, активирующие добавки. Это такие «катализаторы» процесса, они помогают цинку активнее проникать в сталь. Ну и инертные наполнители – они нужны, чтобы порошок не спекался в процессе нагрева и обеспечивал равномерное покрытие. Вот так, если коротко, и происходит этот волшебный процесс.
Итак, мы разобрались, как происходит сам процесс термодиффузионного цинкования. Теперь давайте посмотрим, что же получается в итоге, когда деталь выходит из печи. Ведь главное, это какие свойства дает такое покрытие, правда?
Самое интересное в этом покрытии – это его структура. Вы же помните, я говорил, что цинк не просто налегает сверху? Он проникает внутрь. Так вот, покрытие это не однородное. Оно многослойное, и каждый слой – это своя интерметаллидная фаза. Представьте себе такой слоеный пирог, где каждый слой имеет свой уникальный состав железа и цинка. Обычно там выделяют фазы Г (гамма), дельта1, дзета и эта. Ближе к стали – больше железа, ближе к поверхности – больше цинка. И вот эта многослойность, этот плавный переход от стали к цинку, обеспечивает просто феноменальную адгезию. То есть, покрытие держится на металле неимоверно крепко. Его очень трудно отслоить, это не как краска, которая может облупиться. Оно буквально срстлось с основной сталью. И вот именно из-за этой структуры и появляются все те замечательные свойства, о которых так много говорят. На первое место, конечно, выходит коррозионная стойкость. Это покрытие выдерживает агрессивные среды, соленые туманы, промышленные выбросы – что угодно. Причем гораздо дольше, чем обычное цинкование. Я сам видел примеры, когда детали после ТДЦ стояли под открытым небом десятилетиями и хоть бы что. И при этом у него очень высокая твердость и износостойкость. Это не мягкий цинк, который легко поцарапать. Интерметаллиды, они же по своей сути керамикоподобные соединения, очень прочные. Соответственно, покрытие отлично сопротивляется абразивному износу. Ну, то есть, если что-то будет тереться об покрытую поверхность, оно не сотрется так быстро, как обычный цинк. И, что очень важно, оно устойчиво к механическим повреждениям. Ударили, поцарапали – если покрытие не пробито до стали, оно все равно будет работать как защита. Это потому, что оно не отслаивается по краям царапины, как это часто бывает с другими покрытиями.
Еще один огромный плюс – это равномерность покрытия. Вот попробуйте оцинковать горячим способом какую-нибудь сложную резьбовую деталь, да еще и с внутренними полостями. Скорее всего, где-то будут наплывы, где-то цинк просто не затечет. С термодиффузионным цинкованием такого нет. Порошок проникает везде, куда попадает воздух. То есть, резьба остается четкой, все углубления покрываются равномерно. Это просто незаменимо для крепежа, например. И, конечно, не могу не упомянуть об экологичности. Это «сухой» процесс, нет никаких ванн с химикатами, никаких вредных стоков. Это прямо большой плюс для природы, и для производства тоже.
Если сравнивать с другими видами цинкования, то ТДЦ, на мой взгляд, часто выигрывает.
- Горячее цинкование дает толстый слой, но он может быть неоднородным, и есть риск деформации тонкостенных изделий. Да и вид у него такой, «шагреневый».
- Гальваническое цинкование – это тонкий, достаточно хрупкий слой, склонный к водородному охрупчиванию, да и коррозионная стойкость у него похуже.
- Холодное цинкование – это, по сути, покраска цинксодержащей краской, это вообще другая история, и стойкость там, мягко говоря, не та.
Преимущества термодиффузионного цинкования
Ну, раз уж мы заговорили о сравнениях, давайте четко выделим все преимущества термодиффузионного цинкования. Это, знаете ли, целый список.
Самое главное – это, конечно, долговечность защиты от коррозии. Покрытие служит очень и очень долго, часто в разы дольше, чем другие виды цинкования. Для изделий, которые эксплуатируются в агрессивных условиях, это просто спасение. А если учесть, сколько стоит замена или ремонт, то экономия получается просто огромной.
Как я уже говорил, возможность нанесения на изделия сложной формы – это прямо суперспособность ТДЦ. Всякие уголки, внутренние поверхности, резьба, мелкие детали – все покрывается равномерно и без проблем. С этим, ну, другие методы часто пасуют.
Очень важный момент для высокопрочных сталей – отсутствие водородного охрупчивания. При гальванике, например, атомы водорода могут проникать в структуру металла и делать его хрупким. Это опасно для крепежа, например, он может просто лопнуть под нагрузкой. При ТДЦ такого не происходит, потому что нет электролита. Соответственно, сохраняются механические свойства стали. Прочность, твердость, пластичность – все остается на своих местах. Это не как при горячем цинковании, где иногда высокопрочные стали могут потерять часть своих свойств из-за высоких температур.
Еще один, на первый взгляд, неочевидный, но очень ценный плюс: на термодиффузионное покрытие можно потом наносить лакокрасочные покрытия. И держатся они на нем гораздо лучше, чем на других видах цинка. Почему? Поверхность интерметаллидов пористая, и краска, грубо говоря, «цепляется» за эти поры. Плюс, нет оксидной пленки, как на горячем цинке, которую нужно специально удалять перед покраской.
В долгосрочной перспективе, это экономическая эффективность. Хотя начальная цена может быть и выше, чем у простой покраски, но если посчитать жизненный цикл изделия, то ТДЦ оказывается гораздо выгоднее. Не нужно часто перекрашивать или менять детали. Ну и, конечно, экологическая безопасность. Без токсичных отходов, без выбросов – это сейчас очень ценится.
Где применяют термодиффузионное цинкование
Где же используется эта замечательная технология? Да практически везде, где нужна надежная и долговечная защита от коррозии! Это не преувеличение.
Начнем со строительства. Тут ТДЦ просто находка. Всякий крепеж – болты, гайки, шайбы, анкеры – все это подвергается воздействию влаги, химии. И термодиффузионное покрытие обеспечивает им долгий срок службы. Металлоконструкции, арматура для железобетона, закладные детали – тоже. Ведь если ржавеет арматура, это очень опасно для прочности всей конструкции.
В автомобильной промышленности тоже находят применение. Детали кузова, которые скрыты от глаз, но подвержены коррозии от дорожных реагентов, элементы подвески – тут ТДЦ дает хорошую защиту. Особенно это касается элементов, которые труднодоступны для других видов покрытия.
Энергетика – это огромная сфера. Опоры ЛЭП, элементы подстанций, различные крепежи для оборудования – все это работает в очень сложных условиях, под открытым небом, часто в агрессивной среде. Надежность здесь превыше всего, и ТДЦ ее обеспечивает.
Нефтегазовая промышленность – тут, наверное, самые жесткие условия. Трубопроводы, оборудование на буровых установках, в насосных станциях – все это контактирует с агрессивными средами, высокими температурами. И тут к ТДЦ предъявляют высокие требования, и оно их, в общем-то, оправдывает.
Для железнодорожного транспорта это тоже актуально. Детали вагонов, крепления рельсов – все, что постоянно находится под нагрузкой и подвергается воздействию погоды.
Про метизную продукцию я уже говорил – болты, гайки, саморезы. Это же расходный материал, но от его качества зависит надежность многих конструкций.
В сельскохозяйственной технике – машины работают в полях, под дождем, с удобрениями, которые, кстати, часто очень агрессивны. Защита от коррозии здесь очень важна.
Судостроение – это вообще отдельная песня. Морская вода, соленый туман – это просто убийца для металла. ТДЦ помогает защитить детали судов.
Ну и, конечно, городская инфраструктура. Ограждения, уличная мебель, фонарные столбы – все это должно не только выглядеть красиво, но и служить долго, не ржаветь.
Как видите, спектр применения очень широк. И это неудивительно, ведь эта технология предоставляет по-настоящему надежное и долговечное решение для защиты от коррозии, что в нашем мире, полном влаги и химии, просто необходимо.
Добавить комментарий
Для отправки комментария вам необходимо авторизоваться.